
NOVAMEM'S UNIQUE PLATFORM FOR POROUS POLYMER MEMBRANES
Producing porous polymer membranes generally uses a classical phase inversion process by immersing a polymer solution into a coagulation bath. As the polymer precipitates from the solvent, it forms the membrane’s porous structures. The properties of these phase inversion membranes are intricately tied to the coagulation bath’s parameters, such as temperature, solvent composition, and additives.
The consequences are obvious. Achieving specific membrane characteristics, therefore, needs meticulous control and optimization of these coagulation conditions. Just imagine how slowly such a process can be adapted to the needs of our modern society.
This is why we have invented the slash/technology!
Flat sheet membranes
made from a physical template

slash/ offers the following advantages
Novamem harnesses the capability to select polymers with desired properties for tailored membrane performance. Thanks to the innovative slash/ technology, these chosen polymers can be effortlessly transformed into porous membranes. Notably, this technology eliminates the need to modify our manufacturing equipment, irrespective of the polymer chosen. This approach ensures both versatility in polymer selection and consistency in membrane production.
Examples: We process PES, PSU, PU, PI and many more
The slash/ technology innovatively incorporates a physical particle into polymers to influence membrane structure. By varying the size of this embedded template, specific pore sizes can be attained in the resulting membrane. This technique offers unparalleled control, allowing both porosity and pore size to be tailored according to specific requirements. Consequently, it provides a flexible solution to diverse membrane needs without compromising performance.
The membrane's morphology can be modified to cater to specific performance criteria. By crafting a symmetrical structure, high tortuosity can be achieved, enhancing the membrane's selective barrier properties. Conversely, an asymmetric design can balance between cut-off specifications and flow resistance, allowing for a high cut-off with an elevated throughput. This flexibility in design ensures that diverse application requirements can be met without compromising efficiency or function.
In addition to morphological adjustments, mechanical reinforcements can be integrated into the membrane structure to enhance stability. By embedding materials like fabrics or nonwovens, the membrane's overall mechanical robustness is significantly improved. This incorporation not only boosts the membrane's durability but also ensures consistent performance under demanding conditions.
Novamem prioritizes safety and sustainability, offering the possibility to produce membranes using non-SVHC solvents. These membranes are crafted with an emphasis on compatibility to various recognized standards. Specifically, for applications involving drinking water, Novamem membranes can align with established standards such as NSF, KTW-BWGL, and WRAS. This ensures that our products not only deliver optimal performance but also adhere to stringent safety and quality benchmarks.
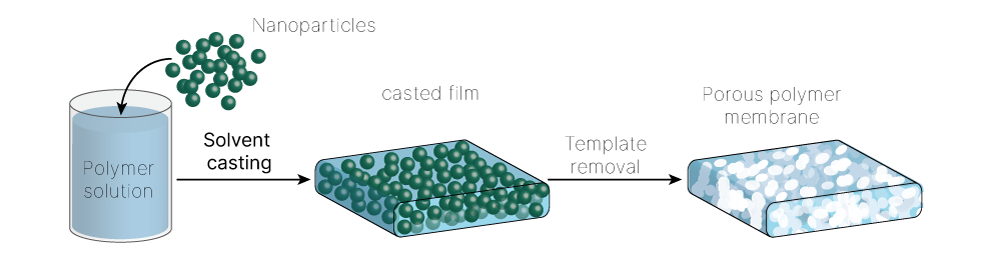
three simple steps behind the slash/ technology
The first step can be compared to traditional lacquer production with procedures familiar in industries like paint manufacturing. Initially, the chosen polymer is dissolved in a selected solvent. Subsequently, the template is incorporated and thoroughly mixed until a uniformly dispersed lacquer emerges. This process, in its essence, is reminiscent of the methods employed to achieve homogeneity in the paint industry.
The lacquer is then meticulously coated onto a substrate, creating a wet film. As this film undergoes a drying process, it solidifies into a distinct structure. This results in a polymer-template composite that firmly adheres to the surface of the substrate. The end product is a stable composite layer.
The template removal process is a crucial step of the slash/ technology. After casting and drying, the film is submerged in an acidic bath, which prompts the dissolution of the template. This action effectively unveils the pores within the membrane structure. Once the membrane undergoes subsequent washing and drying stages, the porous polymer membrane is readily available for utilization.
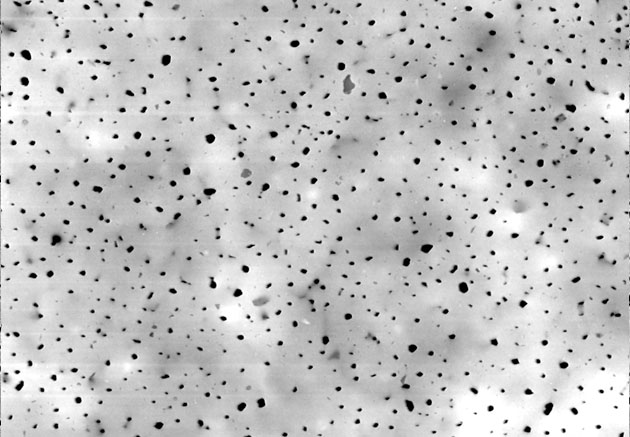
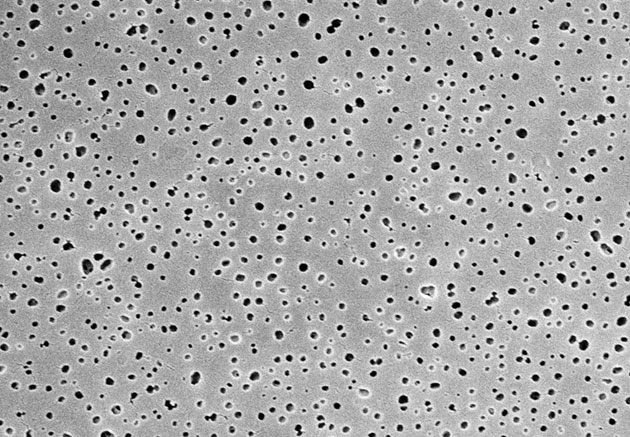